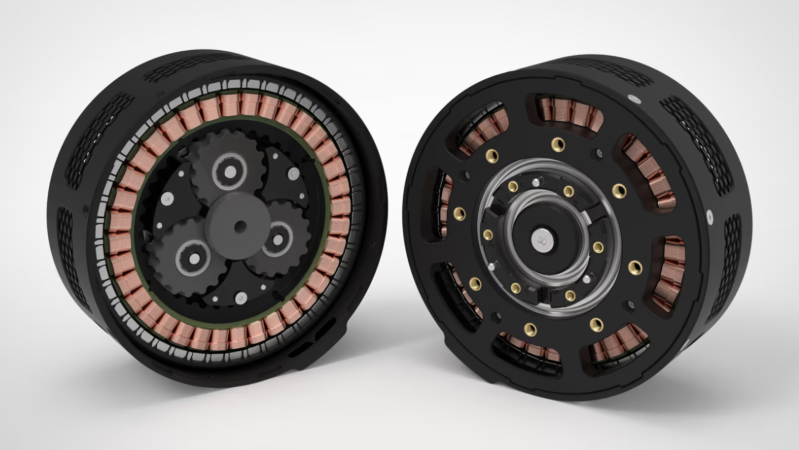
It’s an unfortunate fact that when a scientist at MIT describes an exciting new piece of hardware as “low-cost,” it might not mean the same thing as if a hobbyist had said it. [Caden Kraft] encountered this disparity when he was building a SCARA arm and needed good actuators. An actuator like those on MIT’s Mini Cheetah would have been ideal, but they cost about $300. Instead, [Caden] designed his own actuator, much cheaper but still with excellent performance.
The actuator [Caden] built is a quasi-direct-drive actuator, which combines a brushless DC motor with an integrated gearbox in a small, efficient package. [Caden] wanted all of the custom parts in the motor to be 3D printed, so a backing iron for the permanent magnets was out of the question. Instead, he arranged the magnets to form a Halbach array; according to his simulations, this gave almost identical performance to a motor with a backing iron. As a side benefit, this reduced the inertia of the rotor and let it reverse more easily.
To increase torque, [Caden] used a planetary gearbox with cycloidal gear profiles, which may be the stars of the show here. These reduced backlash, decreased stress concentration on the teeth, and were easier to 3D print. He found a Python program to generate planetary gearbox designs, but ended up creating a fork with the ability to export 3D files. The motor’s stator was commercially-bought and hand-wound, and the finished drive integrates a cheap embedded motor controller.
To test the actuator, [Caden] attached an arm and applied perpendicular force. The actuator only failed on the first test because it was drawing more current than his power supply could provide, so he tested again with an EV battery module. This time, it provided 29.4 Nm of torque, almost three times his initial goal, without suffering any damage. [Caden] only stopped the test because it was drawing 50 A, and he thought he was getting close to the hardware’s limit. Given that he was able to build the entire actuator for less than $80, we think he’s well exceeded his goals.
If you’re interested in the inspiration for this actuator, we’ve covered the Mini Cheetah before. We’ve also seen these drives used to build other quadrupedal robots.
Thanks to [Delilah] for the tip!